Plastic Molding for Electrical Applications
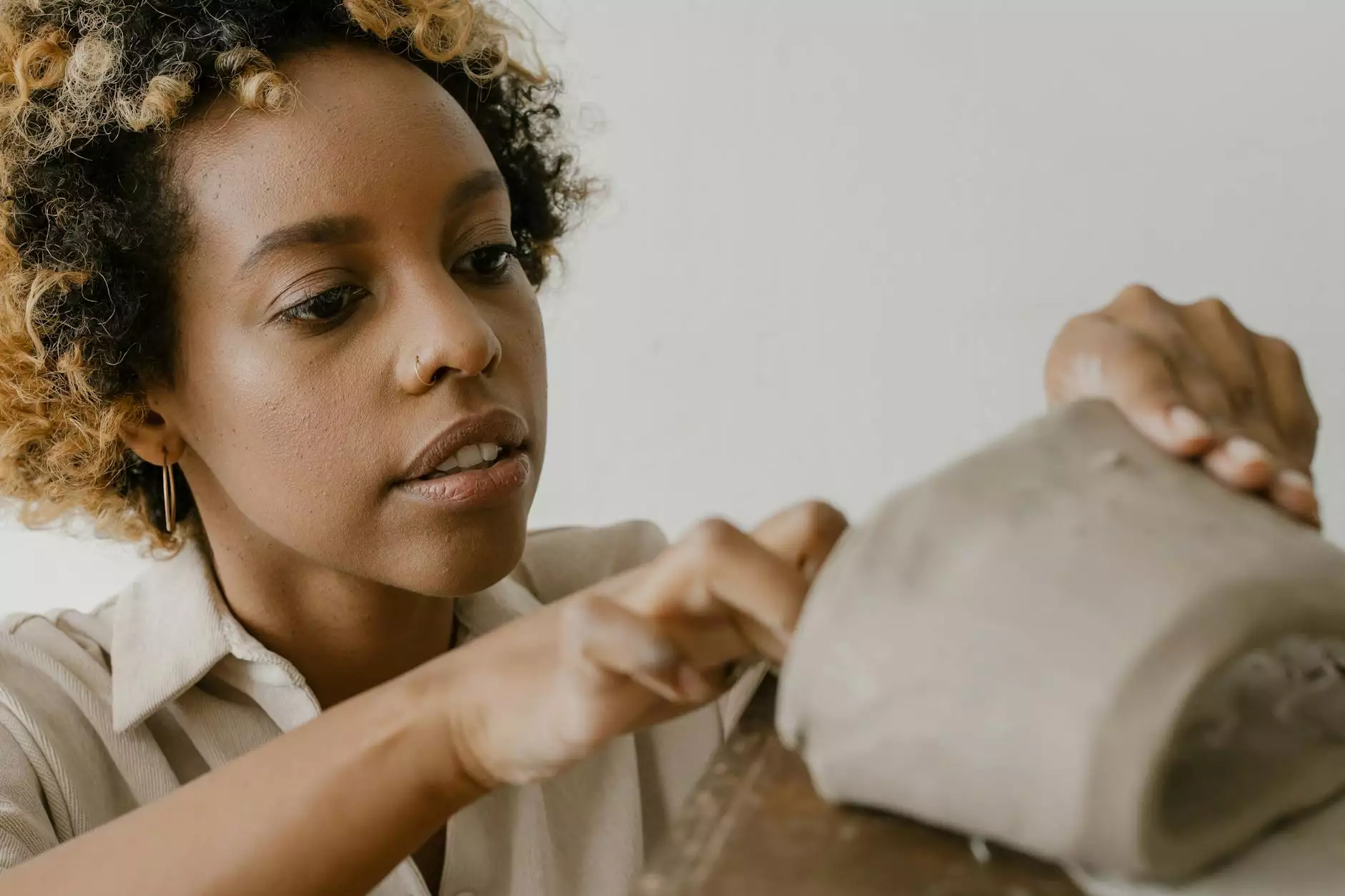
Plastic molding for electrical components has become an essential aspect of modern manufacturing, driven by the need for efficiency, durability, and cost-effectiveness in electrical products. This article delves deep into the world of plastic molding, exploring its significance, processes, applications, and expertise offered by businesses like Deepmould.net.
Understanding Plastic Molding
Plastic molding refers to various manufacturing processes used to create parts by combining raw plastic materials in a mold. The processes can vary, but all share the same fundamental principle: they involve heating plastic to a pliable state, injecting it into a mold, and allowing it to cool into the desired shape. This method is pivotal in producing high-precision components required in the electrical industry.
The Importance of Plastic Molding in the Electrical Sector
In the electrical industry, components must not only be functional but also designed for safety, reliability, and cost-effectiveness. Plastic molding offers numerous advantages:
- Versatility: Plastic molds can produce a variety of shapes, sizes, and designs to meet specific electrical applications.
- Durability: Molded plastics can withstand high temperatures, corrosion, and electrical loads, making them suitable for demanding environments.
- Efficiency: The molding process allows for high-volume production with reduced waste, contributing to lower costs and faster turnaround times.
- Customization: Businesses can tailor their designs and incorporate unique features directly into the molded products.
- Weight Reduction: Plastic components are typically lighter than their metal counterparts, which is advantageous for portable devices.
The Plastic Molding Process Explained
1. Material Selection
The first step in the plastic molding process involves selecting the right type of plastic. Factors such as temperature resistance, strength, and electrical insulation properties play crucial roles. Common materials include polycarbonate, polypropylene, and polyethylene.
2. Design and Prototyping
Before the actual molding process begins, engineers design the component using computer-aided design (CAD) software. Prototyping allows manufacturers to assess the design's feasibility and functionality, ensuring it meets all requirements before mass production.
3. Mold Creation
Creating the mold is critical as it defines the finished product's dimensions and details. Molds can be made from various materials, including steel or aluminum. The choice largely depends on the production volume and part complexity.
4. Injection Molding Process
The actual injection process involves:
- Heating: The plastic material is heated until it reaches a molten state.
- Injection: The molten plastic is injected into the pre-designed mold under high pressure.
- Cooling: The mold is allowed to cool, solidifying the plastic into its final shape.
- Ejection: Once cooled, the molded part is ejected from the mold, ready for further processing.
Applications of Plastic Molding in Electrical Engineering
The versatility of plastic molded components translates into numerous applications within the electrical industry:
- Connectors: Plastic molding is widely used to create robust connectors that ensure reliable electrical connections.
- Encapsulation: Electrical components are often encapsulated in molded plastic to protect against environmental factors.
- Housing: Lightweight and durable housings for electrical devices are commonly produced using plastic molding techniques.
- Circuit Boards: Certain circuit board components are molded to provide insulation and protection from physical damage.
- Switchgear: Many switchgear assemblies integrate plastic molded parts to enhance performance and reduce weight.
Choosing the Right Metal Fabricator for Plastic Molding Needs
Selecting a qualified metal fabricator is vital for successfully implementing plastic molding in electrical applications. Companies like Deepmould.net provide valuable expertise in both plastic molding and metal fabrication, ensuring seamless integration of various materials:
- Experience and Expertise: Look for fabricators with extensive knowledge of both plastic molding and the specific electrical applications you need.
- Innovation: The best fabricators leverage state-of-the-art technology and innovative solutions to improve product quality and efficiency.
- Quality Assurance: A reputable fabricator will have strong quality assurance processes in place to ensure all components meet industry standards.
- Custom Solutions: Each electrical application is unique; a good fabricator should offer customized solutions to meet specific requirements.
- Customer Support: Reliable customer support ensures that any questions or issues during the manufacturing process are promptly addressed.
Future Trends in Plastic Molding for Electrical Applications
As technology evolves, so do the techniques and materials used in plastic molding for electrical applications. Here are some exciting trends to watch:
- Biodegradable Plastics: With increasing environmental concerns, the use of biodegradable plastics is gaining momentum in electrical components.
- Smart Molding Techniques: The integration of IoT in manufacturing processes is leading to smart plastic molding solutions that enhance efficiency and data collection.
- Additive Manufacturing: The rise of 3D printing technology is beginning to influence traditional molding methods, allowing for more complex designs without significant production costs.
- Advanced Composite Materials: The development of composite materials will further improve the performance characteristics of molded electrical components.
- Automation and Robotics: Automated solutions are streamlining the molding process, leading to higher precision and lower production times.
Conclusion
In conclusion, plastic molding for electrical applications plays a crucial role in the manufacturing sector, providing superior benefits in terms of design, functionality, and cost-efficiency. With the ongoing advancements in technology and materials, businesses like Deepmould.net continue to lead the way in delivering innovative solutions tailored to the needs of the electrical industry. As you consider your next project, remember the importance of choosing the right processes and partners to realize your vision in electrical product development.